日常生活のさまざまな場面で「AI」「ICT」「IoT」が活用され始めており、それらは理解が難しい存在から私たちにとって身近な存在へと変わりつつあります。日本のモノづくり企業でも、自社や業界を革新しようと「AI」「ICT」「IoT」などへの取り組みが日々行われています。
しかし、総務省が2019年に公開した「令和元年 通信利用動向調査報告書(企業編)」によると、製造業においてシステムやサービスにIoTやAIなどを導入していない企業は全体の62.6%。導入しない理由は「どのシステムやサービスを導入すればいいのかわからない」「導入後のビジネスモデルが不明確」「コストがかかるから」と、取り組むべきと認識しているものの、自社とそれらがどう結びつくものなのか、イメージすらできていないという状況があります。
参考)総務省 2019年「令和元年 通信利用動向調査報告書(企業編)」
https://www.soumu.go.jp/johotsusintokei/statistics/pdf/HR201900_002.pdf
そういった悩みを持つ企業や経営者に向けて今回は、株式会社smart-FOAの代表取締役である奥 雅春氏に「製造業の企業や経営者は、これからの日本のモノづくりをどのように考えるべきなのか」ということや今までの自身の経験から感じてきたことをインタビューしました。
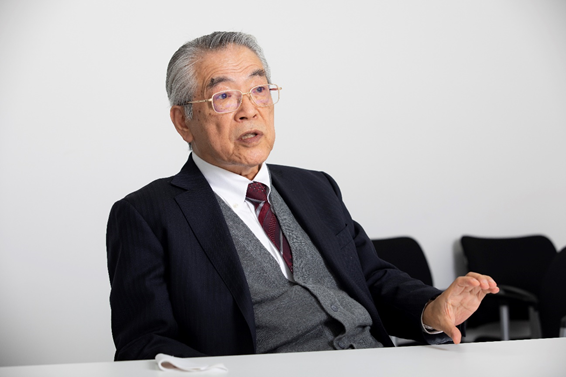
株式会社smart-FOA・奥 雅春氏の経歴
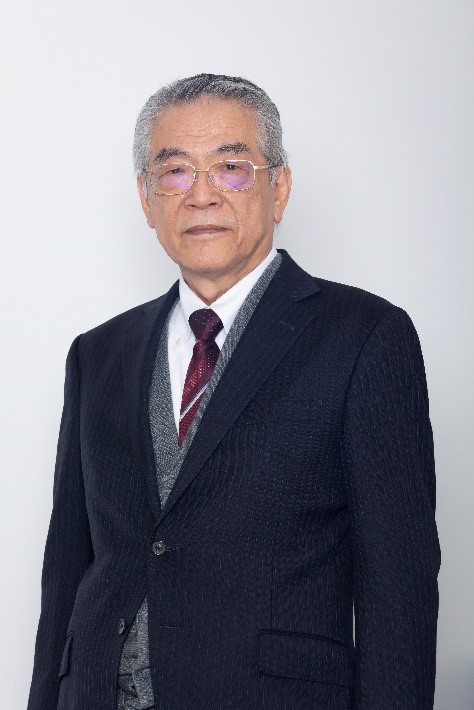
1950年 岡山県生まれ。
1973年 長崎大学工学部電気工学科を卒業後、ブリヂストン社へ入社。タイヤ製造装置部門に配属。生産および製造技術の開発運用を担当
1989年 ブリヂストンが買収したファイアストン社に派遣。
2000年 タイヤ生産技術の取締役へ就任
2002年 取締役常務執行役員への就任
2007年 ブリヂストンサイクル代表取締役会長を兼任
2011年 株式会社smart-FOA(当時、合同会社FOAシステム)を設立
モノづくりの考え方の違いを痛感
――奥社長の経歴のなかで、ブリヂストンに入社後ファイアストン社へ派遣され、実績を残してきたことが注目されやすいかと思います。当時、ファイアストン社への派遣についてはどう感じていましたか?
奥:ブリヂストン本体の3倍ほどの規模であるファイアストン社を買収したわけなので、当時はいろいろと大変でしたね。
製造部門だけでも150人ぐらいの従業員を派遣させることになった。でも多くの人材を派遣させてしまうと、日本に残って仕事する人材もいなくなるためブリヂストン側も大変なわけで。「行くも地獄、残るも地獄」といったぐらいの大変さがありました。
――実際に行ってみた結果、国単位で考えて「日本と海外(アメリカ)ではモノづくりに対して考え方が違うな」と感じた部分はありましたか?
奥:全然違いますよね。私がファイアストン社の件でアメリカに赴任したとき、家族も一緒だったので息子を現地の小学校に編入させました。その学校には「Be independent(独立せよ)」と書いてありました。でも当時の日本は「みんなで仲良く」といっていました。
このことからわかるように、日本は基本的にチームワークを重視していて、仕事にもそれは強く影響しています。それぞれがノウハウを持っていたら「みんなで共有しよう」と考えるのが日本。
ところが、アメリカでは各自ノウハウを持っていても「このノウハウやスキルは俺のもの」と内に秘めておく傾向が強いです。
日本にもそういった考え方はありますが、どちらが良い悪いということではなく「日本とアメリカは両極端な考え方を持っているな」と感じていましたね。
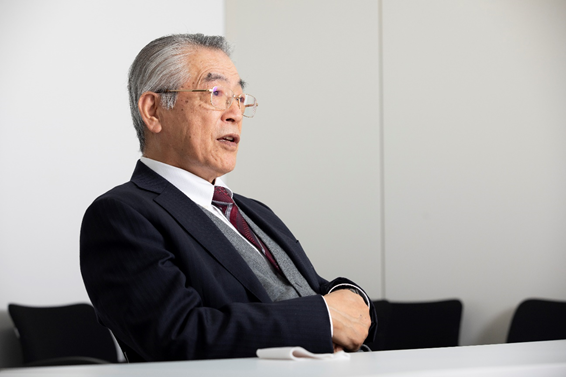
日本流モノづくりを突き通すがスピード感はあがらない
――アメリカと対極な考え方を持っている日本が、アメリカの会社を立て直ししなければならない。当時のファイアストン社の方々に受け入れられたのでしょうか?
奥:基本的にファイアストン社は買収されたわけですから、見かけ上は素直に受け入れてくれますよ。でもだからといって業務をちゃんと進めるかというと、そういうわけにはいかなかったですね。
先ほど「モノづくりの考え方が違うと感じた」と話しましたが、もともと国の制度や思想、宗教観の違いがあるわけです。日常生活のなかでも、テレビで同じ場面を見ていてもアメリカ人は笑えるけど日本人は笑えないといったこともあります。
そういった共感や理解といった部分でズレが生じていたので、仕事においてもそのズレが生まれていました。
――ということは、日本のなかで生まれた“ブリヂストン流”をアメリカの考え方に合わせて何かしらを変えていったのでしょうか?
奥:いや、ダイレクトに持っていきましたね。いわゆるカイゼンというアプローチですよね。悪いところがあったら自分たちで直そうといったアプローチがあって、その代表格はトヨタ社のカイゼンアプローチ。ブリヂストン社にもブリヂストン流のカイゼンがありました。
他にも日本企業は、それぞれ歴史や考え方が微妙に異なるところがあるけれど、根本は「みんなで知恵を出して工夫してカイゼンしていき、それをどんどん積み上げていこう」という考え方。そうすると、モノづくりは強くなる。
カイゼンに取り組んだ人たちは「知恵が出てきて取り組むといいいことあるぞ」みたいなことは肌感覚的にわかっています。そうやってきた結果が、日本のモノづくりの強さとして現れてきたわけです。
しかしこれは理論的ではない。例えばカイゼンしてもどのくらい売上げがあがるのかわからない。「これをやればこれが得られる」ということが明確にあるわけではなく、実践してみてはじめて分かる、思想に近いかなと感じます。
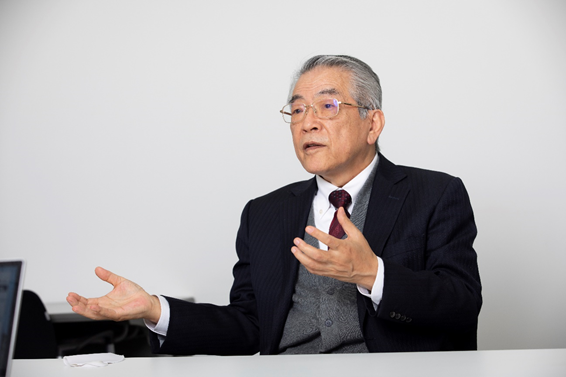
――その思想にも近いカイゼンをダイレクトに持っていった結果はどうでしたか?
奥:全然進まないですよ。時間的にいうと日本の3倍、下手をすると5倍かかっていましたね。実際カイゼンをしても、一緒にやってうまくいったぞとやっても、それが定着するまでを考えると、2歩進んで1.5歩下がるみたいな状況でした。
カイゼンによって改良するというのは「生産性をあげる」「コストを下げる」「品質を良くする」ということですが、アメリカが年間1%改良していたとすると、日本は3%ぐらいの改良が進んでいるような状況。スピード感が全く違うので、その2%の差はちっとも縮まりません。
周りからの追い上げ。そしてFOA誕生のきっかけ
――少しずつカイゼンの取り組みを進めていったと。
奥:そうですね。しかし最近欧米もだいぶ日本に近づいてきたと感じます。他にも中国は日本のいいところを真似してどんどん追いついてきています。
「日本のパクリだ」といわれていることもあるけれど、パクっていてもそこで止まっている人たちを怖く感じる必要はなく、それよりも“次から次に生み出す力”が重要です。
――その先を見ろと。
奥:パクる(真似する)ことを利用して、次から次へ進んでいく人たちが一番怖い。
元をたどれば、日本だって大昔から欧米の技術をパクっているわけですよ。基本的には欧米から全部入ってきているから。でも何が違うかというと、“日本はそれを取り込んで自分たちのものにしていき継続する”そういう世界があるわけですね。
しかし今は周りの国々がモノづくりに対してスピード感があるからこそ、日本は危機感を持ってその競争に参加していかなければならない。まともに競争したらきっと日本はもっと先に進めると考えています。
――日本に戻ってきたあと、自身の考え方に影響したことや吸収できたなと感じるものはありましたか?
奥:アメリカで教えられたことはいっぱいあります。それは直接的に教えられたというより、日本文化で育ったがゆえに気づかなかったところを、海外に出たことで気づかされたということのほうが大きいですね。
ファイアストン社の件に限らず、日本にいてもそうじゃないかなと思いますよ。1年という単位のなかでも、春夏秋冬という4シーズンを通して日々の生活を見たとき、少しずつ違いが見えてきますよね。その違いを「あれ?どこかちょっと違うぞ」と感じ取り、積み上げていくと、他の違いを際立たせてくれて新たな違いにも気づけるようになります。 私(smart-FOA)が今手掛けているFOAも、そういった違いの気づきから誕生しています。
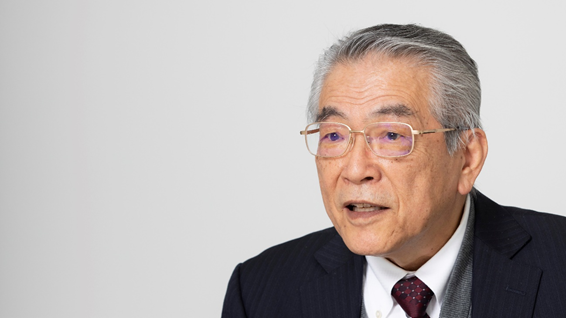
日本流IoT革命が誕生した経緯
――FOAを立ち上げた経緯は?
奥:日本の会社でも経営のやり方はさまざまですが、それは日本の文化や制度、企業風土といったものがベースにした上でつくられたものなので「みんなで一緒にやっていこう」という思想は、基本的に一から説明しなくても理解できる部分がありますよね。
でも話してきたように欧米では同じようにいかない。もっとシステマティックに、ロジカル的に論理立てて伝えないといけないわけです。
例えば、日本だったら「機械で調子が悪い部分があったら、みんなで原因や対応策を考えて...」となりやすいが、欧米の人たちは「いや自分には関係ない。そこはメンテナンス担当の人たちの仕事だから」と事務所に引き上げたりする。
そういった現実のなかで「どうやったら日本のカイゼンをもっとシステマティックにアメリカで進められるのか」というところはずっと考えていました。
――そこからどのようにFOAにつながるのでしょうか?
奥:決していきなりFOAの考え方が出てきたわけじゃなく、当時一番に注目したのはFOAのベースにもなっている“現場のコトバ”です。
製造業の現場で使用されるコトバって「生産性」「品質」「不良率」「総合稼働率」など、数多くあるわけですよ。こういったコトバたちは欧米にも存在はします。ただ、定義の仕方が違います。
例えば「不良率」といったとき、不良になるから不良率になるわけですが、欧米では不良率は最終の出荷時の不良率を指します。そのため、不良箇所を修正することで最終的にOKとなり出荷した場合、それは最終出荷という立場からみたら不良には入らず不良率には影響されません。
ところが日本では「つくった一発目にビシッとつくれなきゃ話にならない」という発想。これをヴァージンアウトといいますが、日本では初期不良率のことが不良率となるわけです。
このように同じコトバでも、英語と日本語だからということではなく、定義が異なっているわけです。この経験から現場のコトバに注目しなきゃいけないなと感じたことがひとつです。
そしてもうひとつは、やはりスピード感を持ってやらなきゃいけないということ。カイゼン活動というのは日々行われるものです。その活動のなかで「あの機械の動作、何かおかしかったよね。昨日はどうだったのかデータで確認してみたい」と、カイゼン活動にデータを活用できないかと感じる部分は昔からありました。マネジメントをやるようになってからも同じです。
――「データの実用をしていく」多くの企業が実現させたいがそれがなかなかうまくいかず悩んでいる課題ですね。
奥:ですよね。実際自社をIT化させようとしたとき、まずはデータをためる。そのあと「こういう目的で使いたい」とプロに伝え、その目的に合うようにグラフ化したり編集したりして使っていくわけです。
でも「その場でデータを使ってください」といわれても、プロではない素人には使えない状態になっている。だからビックデータになればなるほど、人間技ではどうにもならなくなってしまうので、 AI の出番となっている。
でも私としては「それはちょっと違うのでは?」と。「人が使いたいのに人が使えないようにしたらどうしようもないでしょ」と感じました。そこで実際に人がスピード感を持ってデータを使えるようにするために“現場のコトバをデジタル化する”ことからスタートしました。
現場のコトバと実際のデータは違うぞという現実から、データを現場のコトバのレベルに合わせることによって、会話に近い形にしていく。そうすることでさっと使えるじゃないかというのが発想点です。
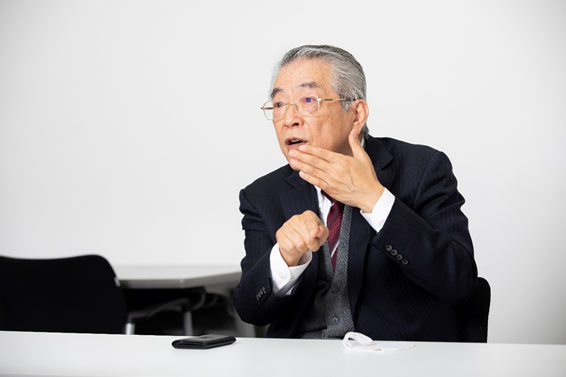
――なるほど。そこから形にしていくにはどういった取り組みをされたのでしょうか。
奥:海外から戻ってきてからすぐにFOAのベースをつくりあげました。具体的に説明すると「現場で異常が起きたぞ」といったことをイベントや事象といいますが、事象が起きたタイミングでそれらのデータを短期間だけサーバーにためておくようにしておきました。
そうやってデータをためていくと発生した場所や時間だけではなく「誰がつくったのか」「オペレーションしていたのは自動モードだった」といったおまけのデータもついてき始めていました。
10年経って私がブリヂストンを引退しようとしたとき、それらたまっていたおまけのデータが「いつどこで誰が何をどうした」といった5W1Hのような形になっていると気づきました。そこで先ほど話した現場のコトバとデータと組み合わせた5W1Hをセットにしたメッセージで整理をすれば、さっと使える情報になるのではないかというのがFOAのコンセプトです。
「とりあえずデータを集めよう、あとからどう使うかを考えよう」ではなく、現場のコトバとして、すぐさま使えるようにデータを情報化(=ストーリー化、5W1H化)してしまえと。
日本のモノづくりのIoTは進むのか
――日本のモノづくりの現場で「もうちょっとこんな風に考えたほうがいいのでは?」や「こういうことが課題だな」と感じる部分はありますか?
奥:もう捉え方がちょっと間違っていますよね。どういうことかというと、今はデータやIT を使うときに、まず仮説を立てそれをデータで検証しようとしますよね。これは間違ってはいないが、ITで検証という形ばっかりになってしまっている。
そうではなく、ある一定の量のデータが出てきたら「こういうことにデータを使いたい」というニーズが出てくるのだから、そのニーズのためにまずは使うこと。また、これからどんどんIT化が進んでいくと「ニーズがあるから使う」だけではありません。データが教えてくれるという発想に立たないといけない。つまり、データを見て仮説を立てるということ。
例えば今の子どもはスマートフォンを普通に使いこなしますよね。でもあれって「生活をしているなかでスマートフォンのニーズがあるから使っている」ではなく「生活のなかにスマートフォンが当たり前に存在していて必要である」ということを最初から認識しているため、コトバを話せないような子どもでもさらっと使いこなすことができているわけです。
大人たちも「ニーズがあるからIT化を目指す 」という発想だけじゃなく「それはもう必要なことで、データがもっとさまざまなことを教えてくれる」というところまでいきついてほしいと思っています。
違うコトバで極端にいうとするならば、現場の事実(データ)が新しい“なぜ“を教えてくれるという観点に立ちましょう。そのようにものの捉え方をしないと、これからのきちんとしたITの使い方になりません。
もっといえば、なぜスマホが当たり前に使えるかといったら、あれはデータを扱っているわけではなく、情報を扱っています。他人のメールを見たって内容がわからないことはあるけれど、文章そのものは理解することはできる。もともと理解できるもの(=情報)が流れているからです。
現場のデータもこういう形があるモノのメッセージ(=情報)にしてしまえばいいわけで、これを5W1H化やストーリー化としています。そういった会話に近い状態をIT でなるべくつくれないかというのが、FOAの発想につながっていきます。
――なるほど。奥社長のモノづくりへの考え方、FOAの根源を理解することができました。
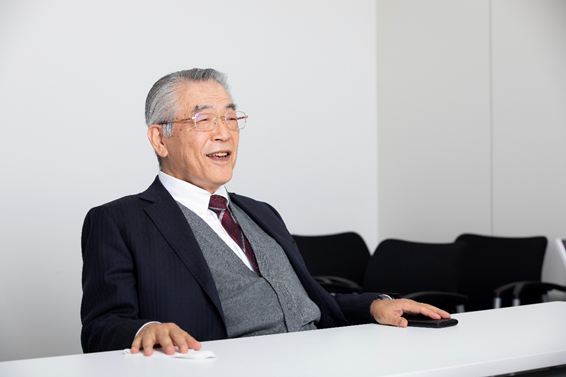
これからデジタル化は避けられない
ではさいごに、ITやAI化なども含め、これから挑戦したいというモノづくりの経営者の方々に対してメッセージをお願いします。
奥:モノづくりの経営者に対して伝えたいのは「やっぱりデジタル化はもう避けて通れなく、絶対に必要ですよ」ということです。先ほど話したようにニーズや費用対効果だけでIT をみる時代はもう終わっています。情報(現場の事実)が次のビジネスのヒントを与えてくれると考えることが大切。
欧米はその事実をつかまえるために、トップダウン型でAIを使い圧倒的勢いでIoT を進めています。ところが日本は、現場が考えるようになっているため歩みが遅くなっている。上がやれといってもやらないし、自分たちでやるとなっても費用対効果、費用対効果というやかましいことを周りからいわれてしまうため、なかなか進まないという現状があります。
――確かにそういった事実はよく耳にしますね。
奥:だからトップも意識を持って現場任せにしないこと。なぜかというと変革だから。変革はマネジメントがやらないと無理。今はトップが現場をリードしなきゃいけない時代です。もちろん現場を無視しない形で。
いくらカイゼンの優秀な人でも、経営全体から見たときのカイゼンやITの重要性は見えないですからね。「そういった視点を持たないともう生きていけませんよ」ということを改めてモノづくりの経営者の皆さんに伝えたいです。
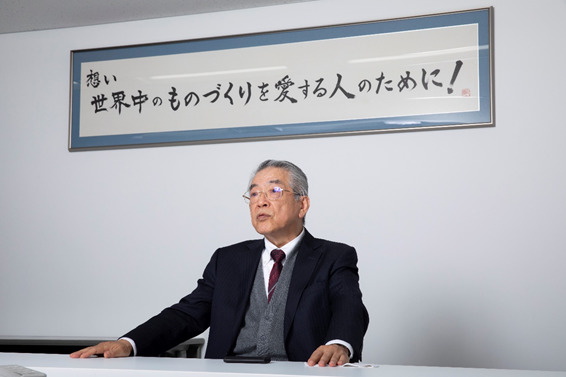
さいごに
――海を越えた国での経験を通して、新たなモノづくりの考え方を築き上げてきた奥 雅春氏。自身の考え方を強く反映させたFOAについても、相手がより理解できるようにその場でお互いが通じるコトバに変え、さまざまな例で説明してくれたのがとても印象的でした。
IoTやAIを取り組むべきと頭で理解はしているがなかなか動き出せていない経営者の方にとって、改めてその重要さを感じ参考になる部分があったでしょう。
今回奥氏は「経営者にこそ、製造の現場のデジタル化は避けられないことを意識してほしい」と強く伝えていましたが、現場の人間もその点を強く理解し経営者とともに今後のモノづくりを生き残っていってほしいと感じました。